Service
Bateq Engineering B.V. supplies full service concepts to keep and support machines its complete life cycle time in optimal condition. Many customers “outsources” service and maintenance work to focus more on their “core business”.
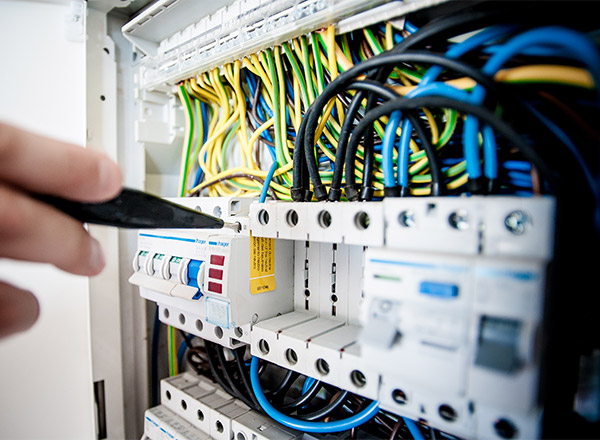
our service and
maintenance group
is your address
partner
The base of our service technicians is our workshop in Almelo.
All our employees have a VCA diploma and have fully equipped service cars at their disposal to carry out the planned work completely and properly.

Our service and maintenance group is your contact partner to coordinate these various activities with you. They can take the desired and/or necessary actions in consultation with you.
In the Netherlands we can usually be on-site within three hours, but this largely depends on the distance and the availability of any personnel and/or parts.
our service and
maintenance group
is your address
partner
The base of our service technicians is our workshop in Almelo.
All our employees have a VCA diploma and have fully equipped service cars at their disposal to carry out the planned work completely and properly.

Our service and maintenance group is your contact partner to coordinate these various activities with you. They can take the desired and/or necessary actions in consultation with you.
In the Netherlands we can usually be on-site within three hours, but this largely depends on the distance and the availability of any personnel and/or parts.
24/7 Support
In the unlikely event that your machine fails, the BATEQ service department supports 24/7 and are available outside our regular office hours. BATEQ can provide you three service levels.
1st Line service
Operators and/or the technical department of the end users resolve any problems with BATEQ equipment themselves, BATEQ takes care of all preventive maintenance.
2nd Line service
When customers technical department can`t resolve a malfunction within a reasonable period of time, they can call on our service department 24/7. By telephone or logging into the operating system our specialists can analyse or watch “remotely” the machine and his malfunction within a relatively short time. The outcome with will be communicated with the technical department who can take the necessary actions to solve the problem.
3rd Line service
In the exceptional case that our service department can`t resolve the problem after the above lines, a specialist will go on site and try to solve the problem on-site.
Good and regular maintenance is important
Maintenance and inspections
BATEQ offers service contracts to help customers manage maintenance costs and to bring reliability of equipment to a higher level. This includes preventive and corrective maintenance.
Good and regular maintenance is important, herewith you can reduce the risks of unplanned down time, production loss, production damage and/or other inconvenience.
Every year agreements will be made between users with regard to annual maintenance visits.
These agreements are recorded in a schedule so customers known in advance when maintenance will be carried out. The intervals of this maintenance are various and depends on the number of production hours, the production environment, the product to be processed, the type of machines, the input and organization of the maintenance service of the end user himself, etc.
For all service agreements, a specific machine report is drawn up at every visit, this report will be kept by us in the machine history. It indicating which parts have been replaced and / or recommendations of work that should be carried out during a subsequent maintenance (or earlier) are carried out. The frequency and extent of the maintenance intervals is determined annually on the basis of available data.
BATEQ wants to “relieve” its customers and offers them the option of entering into a service agreement when purchasing a machine. A service agreement is custom-made, our consultants are happy to inform you about our possibilities.
Fast delivery of original spare parts
Supply of original spare parts
BATEQ has its own production and assembly facilities, which means that we are able to produce quickly. By “night supply” means that our service engineers can have the required parts the next day.
Many common and standard parts are stored in our “ grab stock”. We advise you to keep the specific “Long Leads” and the “Recommended” spareparts in stock so that you never miss out.
For this you can consult the recommended spare parts list which is included in the manual.
Usually these parts can be replaced relatively quickly and can minimize unexpected downtime.
We use an efficient tracking system for the parts used, when you make a request we always strive to provide you with the required information within 2 hours of the first request.
Remote monitoring of machine performance
Installation and commissioning
OEE Tool
The “remote monitoring” of machine performance. Monitoring your production 24/7 where you receive and can use a lot of information to organize your production even more efficiently.
And many other questions that often remain unanswered become clear. With our OEE Tool the total line performance of a process can be made transparent.
BATEQ can completely unburden you, apart from supplying machines and systems we are also able to carry out the entire process of transport, unloading, installation and commissioning on-site for you. After commissioning, training machine operators and technical staff is also possible.
Decline of the KPIs (Key Performance Indicators) are immediately visible and can be anticipated quickly. Any action, malfunction or standstill can be logged and analysed. It is important that inconsistent data by e.g. manual data entry is avoided / prevented.
The actual performance can be analysed on the basis of available information, so the status of processes is immediately visible.
In this way, for example, preventive maintenance can be better planned and downtime due to malfunctions and/or defects can be reduced.